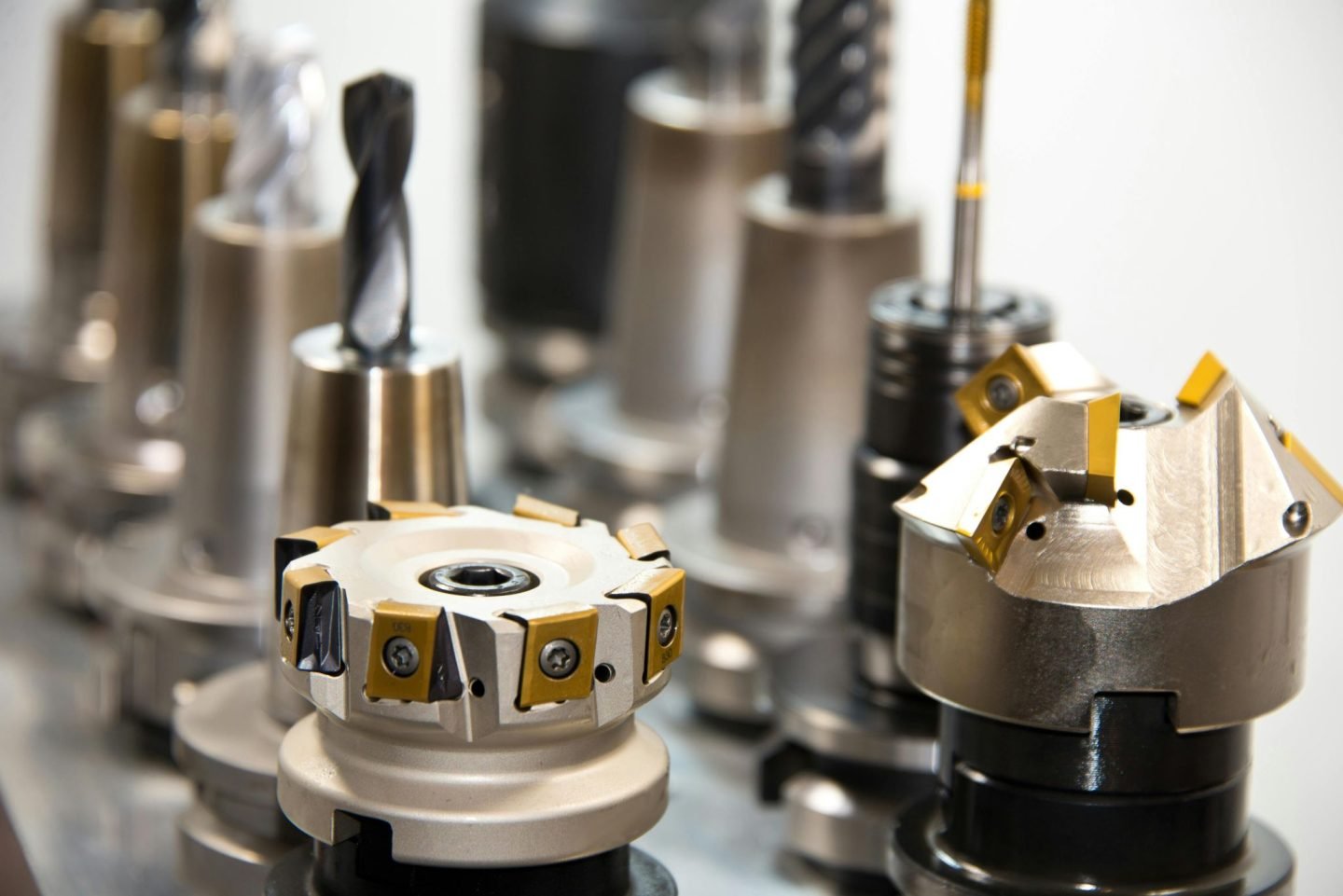
How to Choose the Right End Mill for Steel?
Using the appropriate end mill is crucial in achieving optimal results when milling steel. Carbide end mills, as well as high-speed steel (HSS) end mills, are two common end mills used in steel machining. The decision to use HSS or Carbide end stands alone instead of being dual benefit. Therefore, both end mills should be closely examined to pinpoint distinctions and which one of them is more suitable for a particular application.
If you are looking for more information about steel milling bit – SAMHO, go here right away.
Carbide and HSS Material Selection
The option between carbide and HSS end mill is primarily determined by the intended application. Tools with the expectation of extended operational lifetime are more optimal alongside a larger budget. Carbide end mills are superior in strength and durability, making them a go-to for high-speed and high-temperature steel machining processes. Unlike carbide end mills, HSS end mills can be used in diverse activities, increasing cost efficiency. For enhanced effectiveness and suitability, material hardness, cutting speed, and tool life, aside from other operational requirements, should be thoroughly examined.
For more in-depth information, you should view the steel milling bit – SAMHO.
Understanding Hydraulics’ Influence on Steel Milling Efficiency
When working with steel, the hydraulics of the milling machine, as well as operating parameters, must be taken into consideration. Getting to know the best practices, as well as the influences of hydraulics, can be greatly helpful during steel milling. Among the various aspects to consider are the feeds and speeds of the cut, which, when done correctly, ensure efficient material removal without damaging the tool. Furthermore, the application of coolants during the machining of steel is also crucial as they help to eliminate excessive heat, thus improving the durability of the cutting tool and the quality of the workpiece. Finally, controlling vibration and heat generation are vital in protecting the cutting tool and producing accurate and reliable milling output.
It is possible to achieve excellent steel machining results with CNC projects if one knows the different end mill types, chooses the right carbide or HSS material, and keeps in mind important factors which have a certain bearing to the performance of a milling machine.
What Are the Best Practices for CNC Milling Steel?
CNC milling steel requires the right cutting speed and feed, which greatly increases the tool’s life, workpiece quality, and the entire machining operation. Correct utilization and application selection of coolants has a major impact on machining of any kind, however, these coolants serve multiple purposes such as minimizing friction and heat, ensuring efficient chip evacuation and extending tool life. Proper usage of cutting speeds, applying coolant, and adjusting tool feeds can cut down on tool wear, eliminate the chances of tool damage, control dimensional accuracy, and handle immense surface splashes. It is also important to understand the relationship between cutting parameters and coolants to ensure perfect optimization of the CNC milling process while increasing the effectiveness of machine operations during steel applications.
How to Effectively Use Carbide End Mill in Steel Applications?
Solid Carbide Advantages Over Other Tool Materials
When it comes to steel cutting, solid carbides have numerous upsides when compared with other cutting tools:
- Wear Resistance: Carbide is a very hard material, making it exceptionally wear-resistant, which means it can endure the rigorous engineering controls required during steel end milling. Because of this, the tool will have a longer lifespan, meaning it doesn’t need to be changed often.
- Thermal Stability: Resistant carbide still retains its structural integrity and hardness when being machined. This means that it can be operated in conditions requiring high cutting temperatures, ensuring the precise cut required.
- Increased Productivity: The aggressive cutting edges of solid end mills increase tool chip removal efficiency, ensuring a smoother, cheaper surface. In steel applications, carbide strength can withstand higher feed and cut speeds which means productivity is further enhanced.
Roughing and Finishing Procedures
When using solid carbide end mills for cutting steel, the appropriate roughing and finishing procedures must be used if one wants to achieve the required result.
- Roughing: To rapidly and effectively remove a lot of material, use quicker cut speeds and deeper cuts since these help to reduce machining timing whilst increasing machine effectiveness.
- Completing: Applying lesser feeds and lesser depths while also turning down cuts will achieve higher levels of accuracy and minimum surface imperfections. This method is helpful for accurate engineering and finished steel parts which require critical tolerances.
Detecting Signs of Wear and Damage
It is vital to regularly check the solid carbide end mills to avoid troubles and allow them to perform efficiently. Pay careful attention if the following signs of wear and damage are present:
- Flank Wear: Look for wear on the side or the flank of the tool which can mean it is time to sharpen the tool or change it. High levels of flank wear cause poor finishes and reduces the life of the tool.
- Chipping or Breakage: Examine the edges for chipping or breakage as those will reduce the performance of the cutter and should be repaired as soon as possible.
- Built-up Edge: Be alert to the built-up edge which is visible as a portion of material attached to a cutting edge. Poor evacuation of chips could take place as well as reduced the longevity of the tool could result from it.
These signs should be closely observed and then damaged parts or tools should be repaired or replaced so that steel machining processes using your solid carbide end mills can perform optimally.
What Are the Differences Between Face Mill and End Mill Cutters?
Selection of Facemilling Applications
Facemilling as a technique does not have very many restrictions, for example it can be used to cope up when roughing or squaring off stock. Face milling cutters come in different sizes and arrangements for efficient steel machining operations, which greatly favors the use of this procedure. As far as the flat surfaces are concerned, they can be machined quickly by removing the required amount of material, and this is the main advantage of using this procedure.
Advantages of End Mill for Precision Job
End mills, on the other hand, have several distinguishing characteristics to offer with respect to high precision. For the most part, End mills are bit like drill bits, but they are made with several sharp edges. The presence of multiple shaping edges makes end mills ideal for slotting, profiling, and especially contouring. In steel machining applications where geometry is intricate, End Mills are a great help. Also, in fine finishing and accurate tolerancing, end mills are very important.
Material Removal Rates – A Comparison
As for material removal rates, face milling is likely to rate higher than end milling because it employs a larger cutting diameter and multiple cutting edges that can be used at once. As a result, facemilling is considered to be best suited for roughing operations. The aim of facemilling is fast material removal, which is why it is of great assistance here. In the case of end mills, however, while they are more suitable for applications where precise finishes by removing less material are important but a lot of time would be required to accomplish that.
When deciding on the right tool for steel machining requirements, it is important to know the suitability of face milling and understand the advantages of using end mills. The explanation above indicates that, in order to optimize production, one ought to factor in the end result sought for, material properties and the technological processes that need to be implemented.
Why is Steel Machining Challenging?
Steel alloys come in various sets and have distinctive traits which makes working with steel machining a challenge. Nonetheless, the hardness of the steel is one key aspect that remarkably affects how well a milling machine works. The hardness of steel sets the threshold of cutting forces and abrasion which leads to excessive tool wear or short lifespan of the tools.
As stated before, steel alloys can be differentiated on the basis of their hardness, some can be staggering strong while others are comparatively soft. Sturdier steel’s expected to show better results in terms of strength and longer usage; nevertheless, the steel milling process is more intricate; with sturdy steel, the tools are more likely to be worn out, and there would be a decline in the speed of cutting, and there is a greater surge of heat, and the tools would vibrate more.
How to Maintain Heat and Vibration While Milling
Vibration and overheating are two severe issues that need to be resolved when one works with steel. If a high amount of heat is generated, it is very reasonable for the tools to get damaged, wear off too early, and even deform the material. All of this leads to disastrous effects on the overall quality. If the steel is being built in a piecemal fashion, it can be cut and shaped according to the requirements, this can easily increase the chances of and results in overheating.
There are several options to minimize heat and vibration. The application of coolant or lubricant can drastically lower friction, enhancing tool life and machining accuracy. Also, making use of appropriate machining conditions such as feed and speeds will lower the amount of heat generated. There are also specific milling tools made for steel machining that can improve heat and vibration control; these can help ensure all outcomes are consistent.
By realizing the effect that steel hardness would have on a milling tool and applying suitable methods of heat and vibration management, it is possible to tackle the issues associated with steel machining and improve the efficiency of your milling operations.